Vapour Degreasing Solvents
Vapour degreasing is an advanced solvent cleaning process, used to remove contaminants such as grease, oil, and other residues from metal and other surfaces, commonly used in industries such as electronics, aerospace, and precision manufacturing.
EnviroTech Europe manufactures vapour degreasing solvent cleaners which are widely regarded as the best in the industry, and each of our products exact to high standards in accordance with strict quality control procedures.
A wide variety of solvent blends and derivatives are available for a vast array of applications and industries and they are widely recognized as the premier general use solvents. In addition, we continue to research and develop new products and applications.
Our vapour degreasing solvents are specifically formulated to address the difficult precision cleaning problems experienced in high-tech industries where exceptional levels of cleanliness are needed, and we provide excellent customer service, technical support and training from qualified distributors worldwide.
Introducing ProSolv®5408e , a next generation PFAS free fluorinated solvent offering low GWP and zero ODP.
ProSolv®5408e is a next generation PFAS free fluorinated solvent offering low Global Warming Potential (GWP) & zero Ozone Depletion Potential (ODP). A general multi-purpose vapour degreasing cleaning solvent that can act as an immediate drop-in replacement for most of the 3M™ Novec™ engineering fluids. We can also deliver an exact formulation replacement of your current solvent should that be your requirements.
Featured Product
High performance vapour degreasing solvent
ProSolv®5408e is a new solvent blend from EnviroTech Europe which ticks all the boxes with the perfect profile for a vapour degreasing solvent. Soft on the environment and safer for users. High performance, improved cleaning, lower costs. Sustainable and secure for future use as your forever solvent.
Lower boiling point, economical with energy with low solvent losses, faster production, reduced costs, easy handling. Exceptionally low surface tension to penetrate micron sized holes and close contact surfaces. ProSolv®5408e is the perfect replacement for hazardous solvents such as trichloroethylene, nPB (n-propyl bromide), perchloroethylene or flammable solvents used in general engineering cleaning processes.
Featured Article – ProSolv 5408e sustainable cleaning solvent for vapour degreasing in the aerospace industries… Read more
Featured Topics
Condensation Cleaning: The Future For Solvent Degreasing Equipment
New study confirms 100ppm safe limit for EnSolv
ACGIH’s Threshold for nPB Solvent
United Nations Ozone Assessment
We can provide you with a Material Safety Data Sheet, independent laboratory reports, product samples or technical assistance. For more information or advice please contact us by telephone on +44 (0) 20 8281 6370 or use our contact form.
Vapour degreasing solvents are supplied and supported by EnviroTech Europe Ltd. Manufactured in the United Kingdom and available on short delivery times through our dedicated team of distributors worldwide.
Share this page:
New Products
Vapour Degreasing Cycle Video
Featured Product
Vapour degreasing solvent for precision metal cleaning
A methylene chloride based solvent with a unique blend of surfactants giving it a superior cleaning quality.
This formulation builds on 30 years of experience supplying the EnSolv® range of powerful and reliable vapour degreasing solvents to industries worldwide.
EnSolv CC-A® responds to the need for high performance vapour degreasing solvents for critical cleaning in general engineering, aerospace, medical optical and electrical industries.
EnSolv CC-A® contains a proprietary blend of inhibitors and stabilisers for the solvents to prevent water staining and corrosion of yellow metals such as copper, brass and bronze which can be a problem with some other solvents. Removes oil, grease and soils fast. Read more…
Applications and Case Studies
Featured Article – Vapour degreasing in engineering, aerospace, medical & electrical industries… Read more
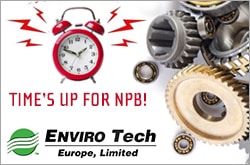
Deadline for solvents needing authorisation was July 2020
Are you still using 1-Bromopropane (n-propylbromide or nPB) for Vapour Degreasing? nPB needs authorisation for use from Sunset date July 2020.
Click here for nPB replacement.
Are you still using trichloroethylene (Trike) for Vapour Degreasing? Trichloroethylene needed authorisation for use from Sunset date 21st April 2016. Click here for trichloroethylene replacement.
Vapour degreasing is an advanced solvent cleaning process, used to remove contaminants such as grease, oil, and other residues from metal and other surfaces, commonly used in industries such as electronics, aerospace, and precision manufacturing.
Our vapour degreasing solvents are widely regarded as the best in the industry. Each of our products exact to high standards in accordance with strict quality control procedures. Read more.
High Performance Vapour Degreasing
ProSolv5408e® is a new solvent blend from EnviroTech Europe which ticks all the boxes with the perfect profile for a vapour degreasing solvent. Soft on the environment and safer for users. High performance, improved cleaning, lower costs. Sustainable and secure for future use as your forever solvent.
Lower boiling point, economical with energy with low solvent losses, faster production, reduced costs, easy handling. Exceptionally low surface tension to penetrate micron sized holes and close contact surfaces. ProSolv5408e® is the perfect replacement for hazardous solvents such as trichloroethylene, nPB (n-propyl bromide), perchloroethylene or flammable solvents used in general engineering cleaning processes.
Vapour degreasing solvent for precision metal cleaning
A methylene chloride based solvent with a unique blend of surfactants giving it a superior cleaning quality.
This formulation builds on 30 years of experience supplying the EnSolv® range of powerful and reliable vapour degreasing solvents to industries worldwide.
EnSolv CC-A® responds to the need for high performance vapour degreasing solvents for critical cleaning in general engineering, aerospace, medical optical and electrical industries.
EnSolv CC-A® contains a proprietary blend of inhibitors and stabilisers for the solvents to prevent water staining and corrosion of yellow metals such as copper, brass and bronze which can be a problem with some other solvents. Removes oil, grease and soils fast. Read more…
Featured Article – Vapour degreasing in engineering, aerospace, medical & electrical industries… Read more
Featured Topics
Condensation Cleaning: The Future For Solvent Degreasing Equipment
Vapour degreasing is the simplest and most effective degreasing and cleaning process.
New study confirms 100ppm safe limit for EnSolv
Update on a safe occupational exposure level for 1-Bromopropane.
ACGIH’s Threshold for nPB Solvent
What You Should Know about the ACGIH’s Threshold for nPB Solvent.